A carbon disc is made up of carbon fibres. When the temperature of the disc is above 700°C, the disc “glow”, the carbon fibres vaporise and air pockets appear. The oxygen that gets between the fibres acts as an insulator. This means that the disc consequently has:
- Poorer thermal conductivity (does not dissipate as much heat as it would otherwise)
- Reduced rigidity (uneven braking feel)
1. MECHANICAL PROCESSING
The disc is disassembled, weighed, measured with a wear gauge, inspected for structural damage and, if necessary, X-rayed. This way, structural damage that is not visible to the naked eye can be identified.
We also clean off any residue of brake linings and other contaminants and prepare the disc for further processing.
Brake discs are then impregnated with polymers to fill the air pockets. This process is repeated until the disc reaches its target weight.
After impregnation, we also check whether the disc core is strong enough to continue the process.
2. FILLING
3. INTERNAL PROTECTION
In the third step, the carbon fibres are “coated” to protect them from further vaporisation.
4. EXTERNAL PROTECTION
We apply an OXY COATING to the outer surface. The coating is not applied to the tread surface, only to the outer and inner surface. The coating prevents oxygen from entering the interior of the carbon-ceramic disc. You can choose between two colours: light or dark grey. The red colour in the picture is symbolic and used only for illustrative purposes.
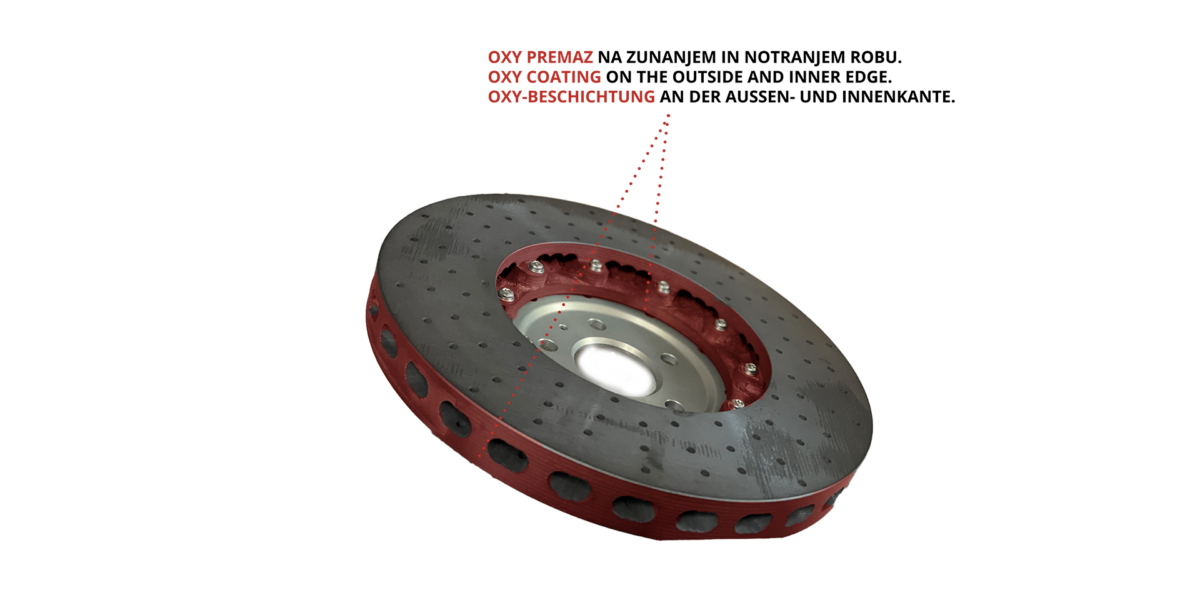
5. FINAL MECHANICAL PROCESSING
Note: The refurbished brake discs are slightly thinner than the original parts due to the repair process, but have a higher density. This means that refurbished discs have a longer lifespan.